Toyota is one of the the automotive companies using additive manufacturing to produce and repair the humble die. The benefits are worth boasting about.
Five to ten years ago, when additive manufacturing (AM) first began finding applications in manufacturing, the value it offered was centered around high-mix, low-volume parts, especially high-cost parts. The classic success story is GE Aviation’s fuel nozzle tip, which delivered massive improvements in efficiency, performance and cost by replacing an assembly of 20 brazed parts with one 3D-printed part. Today, eight years after that part was first produced, AM technologies continue to find new applications in manufacturing.
The additive sweet spot remains high-mix, low-volume parts, because no AM technology today can compete with the production scalability and speed of traditional processes such as molding. At the same time, AM makes possible radical new innovations that aren’t achievable using traditional processes. While the part volumes involved in automaking mean car manufacturers are still waiting for ways to harness the full potential of the latest 3D-printing technology, there’s been meaningful progress in one unsexy but important part of auto production: tool and die repair.
Some noteworthy case studies were revealed by Nils Niemeyer, general manager of additive solutions at DMG Mori USA, in a presentation he delivered at RAPID+TCT 2023, a major tradeshow for additive manufacturing. Niemeyer showed how Toyota and Voestalpine, a VW supplier, are using 3D printing technology from DMG Mori to repair machine parts, thereby saving money and reducing downtime.
Automotive Die Repair using Directed Energy Deposition (DED)
This part is a die used in the production of die-cast aluminum four-cylinder engines for Toyota sedans and SUVs. Using powder-blown DED additive manufacturing, the dies were repaired, providing 300 percent service life for the parts.
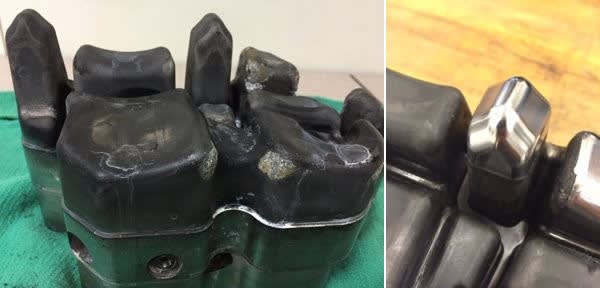
The conventional method for repairing these dies is TIG welding, a labor-intensive process. Engineers developed the new process to incorporate DED on a hybrid five-axis machine from DMG Mori that does both machining and 3D printing.
First, the die condition before repair is measured and assessed, then toolpaths are programmed to remove material on the worn surfaces, cracks and damage. Next, the areas are rebuilt with new metal added using DED. Finally, this material is machined to the final shape. Because this process is done on a single hybrid machine, all three operations are performed in a single setup, which greatly reduces lead time on the repair. The conventional TIG welding process required 96 hours and multiple setups at several workstations. In comparison, the DED process takes 31 hours, a reduction of over 60 percent. In addition, this process avoids transportation between stations. The cycle time for the near-net-shape deposition of material is much faster with DED than with manual welding.
Not only has Toyota achieved these improvements in the repair process itself, but the new repair process also delivers better results. Conventional welding done by humans is subject to human inconsistencies, and as a result conventionally-repaired dies were expected to provide 33 percent additional life compared to a new die. With the AM process done on the hybrid machine, the metal deposition is much more consistent and repeatable. With better quality metal deposition, the parts repaired by the new AM process provide 100 percent tool life, the same as a completely new die.
This provides a significant advantage in the die-casting production process. Because the conventionally repaired dies failed unpredictably, they caused unplanned downtime and required replacements to be kept in inventory. With the new process, die replacement can be scheduled around planned maintenance intervals, as the repaired dies fail predictably, in the same pattern as new dies that have never been repaired.
Another benefit of the new DED process compared to TIG welding is that the DED process has a lesser impact on assessed environmental damage categories than the conventional welding process.
Future Improvements
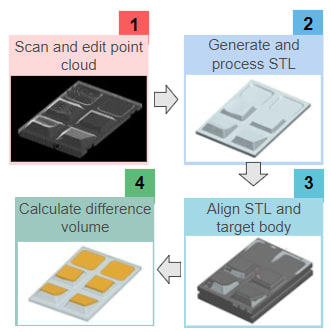
Engineers at DMG Mori see opportunities for future improvements to this process. Specifically, 3D scanning can be used to create a point cloud and an STL of the unrepaired die after surface machining to remove damaged areas. Then, this point cloud can be compared to a digital model of the die. By creating automatic or semiautomatic toolpaths for the near-net-shape DED and final machining processes based on this comparison, the technology will be significantly more adoptable, as this will reduce the need for complex 5-axis CNC programming.
Automotive Die Production using AM Delivers Performance Improvements
As seen in the production of the GE fuel nozzle tip mentioned above, one major advantage of additive manufacturing is that it can produce geometries that are formerly only possible through expensive, multi-step fabrication processes, if at all. This part made by Voestalpine, a European automotive supplier to VW, demonstrates the ROI provided by this capability.
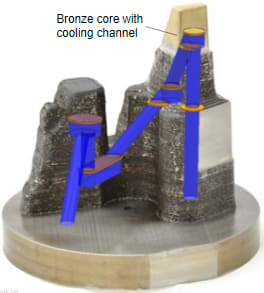
This part was produced on a DMG Mori Lasertec 65 Hybrid machine, which is capable of directed energy deposition (DED) additive manufacturing. This die is used for casting a section of the engine bracket on VW’s 1.8L and 2.0L engine. VW produces 600,000 of these engine bracket parts each year.
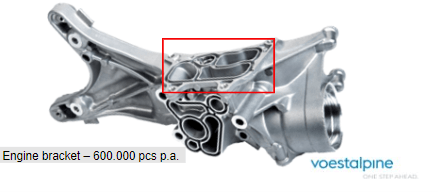
What makes this part unique is the core of the die is made of bronze—which has better thermal characteristics than tool steel—while the outer skin of the part is made from tool steel for durability. In addition, the part has internal conformal cooling channels to more effectively cool the die during operation.
To manufacture this part, the hybrid machine builds up the die in sections. As the first section is finished, the machine comes in with drilling and milling tools to prepare the cooling channels, then builds up the next section using additive tools.
This part offers several advantages over conventionally-produced dies. Thermal imaging shows the conventional die has hotspots which need to cool down, slowing throughput. On the hybrid-manufactured die, the temperature profile is 89 degrees C lower.
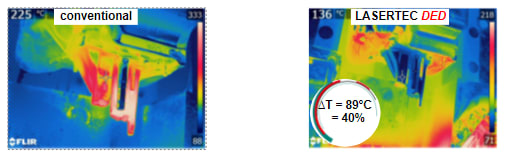
A more homogenous die temperature during operation results in better part quality and higher throughput. X-rays of the cast engine brackets show pores and voids in the material, which leads to scrap parts. With the new die, these pores and voids were eliminated, driving down the scrap rate by 3.3 percent.
While that may not seem like much, since VW produces 600,000 of these engine brackets per year, this saves $183,000 per year on this single part. With the bronze material and the more complex part design, the new die costs only about $800 more, so the ROI is significant.
AM Advantage: Conformal Cooling
This case demonstrates the value of conformal cooling, a strength of additive manufacturing. Conformal cooling simply refers to the design of cooling channels inside mold and die parts that conform to the shape of the part, to provide more efficient cooling to the surface. Because these channels and surfaces don’t follow straight lines, they can’t be drilled.
The key benefit of conformal cooling is reduced cycle time, as better cooling means less time spent allowing the tool to cool down before running the next shot. According to Rock Hill, S.C.-based additive manufacturing technology developer 3D Systems, conformal cooling can reduce cycle time by up to 70 percent. Other benefits include reduced warpage, reduced scrap and reduced surface roughness.