Dieless incremental forming of sheet metal is the high-mix, custom products answer to precision metal stamping.
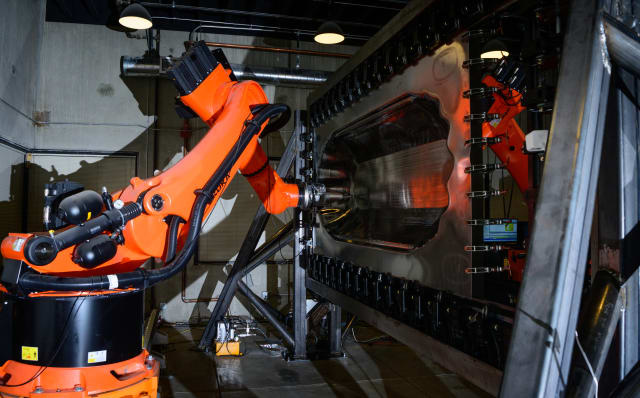
Six axis robots have been a quintessential tool on the factory floor in applications like material handling and spot welding for decades. But as digital manufacturing technology continues to evolve, the industry has seen innovative applications emerge for these precise and accurate robots, including CNC machining, material deposition for additive manufacturing and even dieless incremental forming of sheet metal—also known as roboforming.
That term “dieless” likely made your eyes turn into dollar signs if you’re an engineer looking for new ways to take cost out of a forming process. Just as six-axis is touted as a differentiator for additive manufacturing, the ability of roboforming to produce a part without a die is a key advantage of it and other digital manufacturing processes. Indeed, these digital manufacturing technologies can turn stock material into finished parts without the need for custom tooling, only custom digital instructions.
What is robotic incremental sheet forming (RISF)?
The basic concept of this technique is a robot fitted with a hardened steel, spherical tool which is applied incrementally against the surface of sheet material, typically metal, creating a plastic deformation. Millimeter by millimeter, the deformation is gradually pushed and formed until the sheet stock is coaxed into the part’s final shape, not dissimilar to metal spinning, except without the rotation.
Incremental forming has been done using modified CNC milling machines since the 1990s. However, the advantage of robotic incremental sheet forming is the working area. With a CNC, the part size is limited by the bed size of the machine. If your shop has a large bed CNC machine, you’re likely making too much money operating it as intended to try incremental sheet forming with it.
In the past, roboforming may have been set up with two robots working in tandem, with one robot creating the deformation and another robot on the reverse side of the sheet providing back pressure. However, today’s setups are possible with only one robot. First, the sheet blank is secured in the blankholder (a steel frame). Then, the robot proceeds with the toolpath. Creating the toolpath for the robot requires analysis such as finite element analysis (FEA) to increase the structural integrity of the thin metal sheet. CAM software is also used to generate a toolpath from the CAD model of the desired geometry. For programmers familiar with CNC milling, the additional step of converting toolpath G-code to robot programming commands will be new. However, this is a well-documented process as it’s used in many applications, such as robotic CNC milling. Depending on the brand of robot you have, the vendor (such as FANUC or KUKA, for example) will likely have a software tool to convert the G-code into their proprietary robot programming language. Another option is to use a third-party robot programming software solution such as RoboDK.
Because roboforming does not require custom tooling such as a die, it is a process that supports mass customization—the robot can form 100 different part geometries for the same cost and in the same time as 100 identical parts. However, roboforming is outperformed by traditional sheet forming processes when it comes to mass production at scale, such as a stamping process in the automotive industry, for obvious reasons: per part, a robot moving incrementally is slower than a press.
Robot Requirements for Roboforming
Six axis robots have a much lower stiffness than CNC machines. The robot used for this process must have a high rigidity, which correlates to payload, to avoid deflecting as it exerts force on the sheet metal. The required payload of the robot will depend largely on the thickness of the material. In this study from 2006, Italian researchers Massimo Callegari, Dario Amodio, Elisabetta Ceretti and Claudio Giardini used a a COMAU Tricept HP1 robot, which was able to apply 15 kN of thrust in a working envelope of 2000 mm x 600 mm, with a repeatability better than 0.03 mm.
This video from the Bartlett School of Architecture UCL shows the roboforming process in action.
Why: Benefits of Roboforming
One of the key advantages of roboforming is the low barrier to entry. With the right six axis robot and a competent robot programmer, this process can be set up relatively quickly and easily. As a simple metal instrument, the end effector is not expensive and doesn’t require frequent maintenance. As a dieless process, the lead time from “art to part” is limited only by the programming time. Here are several other benefits of robotic incremental sheet forming:
Precision: automation produces more consistent results than manual processes, reducing scrap rates. In addition, as the geometry is produced incrementally, there is no springback as you may find with other sheet metal forming processes.
Improved safety: while a robotic cell requires safety precautions similar to a press, an automated process can reduce injuries associated with manual handling of heavy and sharp-edged sheet materials.
Mass customization: as a digital process, roboforming produces different parts at the same rate and for the same costs as identical parts, and production can be changed over at the touch of a button.
Small Batch Efficiency: producing small runs of parts with a process like deep drawing is prohibitively expensive. Because RISF eliminates the tooling, batch sizes as low as one are achievable at low cost.
Cost savings: automated forming eliminates high tool and die costs, and may enable the repurposing of a robot not currently applied elsewhere. Roboforming can help optimize production efficiency and minimize waste.
How Roboforming Can Reduce Costs
Digging into the cost advantages of a dieless forming process reveals the specific advantages. First and most importantly is the cost of the lead time required in die production. It can take days to design a die, and weeks to produce it, receive it and get it into production. In addition, dies require regular maintenance such as repair and refinishing past a certain threshold. In comparison, a robotic cell equipped for roboforming can start producing parts before the die would even be cut or cast.
Incremental forming also reduces scrap. Processes such as deep drawing involve trimming scrap from the part. While this scrap can be sold, incremental forming can reduce material cost by 12% compared to deep drawing.
Operation of a press is costly, including lubricants and maintenance. The maintenance and lubrication costs involved in a robotic cell for incremental forming are much lower.
Roboforming Use Cases
Like most other robotic cell applications, roboforming can easily be set up by hiring a robotic system integrator that will design and build the turnkey roboforming cell for customers. Just ask your system integrator about their experience with roboforming or robotic incremental sheet forming. For example, Metal Automation Group, a US-based robotic system integrator, offers a turnkey package for roboforming.
Los Angles-based Machina Labs has developed a software platform for industrial robotics applications including roboforming, and has received funding from aerospace and defense giant from Lockheed Martin Ventures. Robotic sheet forming is the first process enabled by Machina’s manufacturing platform. Using material- and geometry-agnostic technology, the platform outperforms traditional sheet forming methods that rely on custom molds or dies.
“At Machina Labs, we are creating the factory of the future; one where a variety of designs and physical products can be produced on-demand and at scale,” according to Edward Mehr, CEO and Co-Founder of Machina Labs. “With Lockheed Martin’s investment, we can accelerate development of our sheet metal Roboforming to better serve the need of the defense sector and give the United States a competitive advantage in speed of development for national security and defense products.”