How Siemens and Semplor democratized SEM and shrank it to fit on a desk.
Siemens has sponsored this post.
Traditional scanning electron microscopes (SEMs) are large, expensive and complex pieces of lab equipment. To use, maintain and repair them would require specialized knowledge and skills few companies and research outlets have. This didn’t sit well with Semplor, makers of NANOS — an easy-to-use SEM the size of a desktop computer.
Making SEM available to “anybody, anywhere in the world, that’s our goal,” says Emile Asselbergs, CEO and co-owner of Semplor. “Like a modern [cellphone,] you don’t need a training course to use it. It’s easy, fast and doesn’t break.”

The Netherlands-based company achieved this paradigm shift by rethinking SEM technology and designing the NANOS with completely new parts, methodologies and workflows. In other words, they redesigned SEM from the ground up. However, as a small startup, Semplor didn’t have the budget for most engineering design software.
“With Enginia we were in contact about the Solid Edge Startup bundle,” said Asselbergs. “In this period, we were in touch with Enginia about the possibilities of the Solid Edge license, and their customer service helped with the installation and use of [the] Solid Edge Standard Parts Library.”
With this software Semplor made something as complex as an SEM into a machine that looks right at home in any startup, SME, makerspace, big-name research lab and everywhere in between.
SEM experts think the equipment is too complex
Asselbergs explains that traditional SEM equipment can be hard to maintain. “You open them up and they are large, complex, with lots of circuit boards. It needs a lot of maintenance.”
While working in the SEM field, Asselbergs and a few colleagues realized that the equipment doesn’t have to be this complicated. “We’ve been thinking about how to ideally design a table-top SEM. We didn’t use the things of the past or things we didn’t like; instead, we made a new concept,” he says “Organizations have difficulty changing mindsets. That is what we love to do.”
Asselbergs’ colleagues soon became co-founders with a shared goal: to use their combined 200 years of experience with SEM to democratize the field. They understood the common user pain points and wanted to build something better. “It’s what people need these days; when you have a problem, you want to solve it now.”

Aside from the physical design of the NANOS, its software user interface also plays a big role in simplifying SEM. The UI has a lot of automatic functions to optimize brightness, contrast and illumination. It also guides the user through the process so that those new to SEM can catch on quickly. However, it also contains many of the power-user features used by seasoned veterans in the field.
An example of how the NANOS democratizes SEM can be seen with how it deals with living samples. These samples contain a lot of water and are sensitive to the beam of electrons. As a result, they will shrivel in the high vacuum and sustain damage from the beam. Traditional equipment overcomes this challenge by coating living samples in gold, platinum and other expensive materials. Aside from the added expense, this process also complicates the assessment of these sample.
Newer SEMs have an option to operate at low vacuums, which ensures that living samples don’t shrivel and the charge they experience is neutralized. But Asselbergs says this feature is an expensive add-on for traditional SEM offerings. For the NANOS, it comes standard without added expense. This is in part thanks to how the equipment was designed.
“We don’t use vacuum gages, just good calculations,” says Asselbergs. “By the pump power and RPM, we know the vacuum level. Measuring gages cost money and can break, so that’s something we don’t want to use.”
Simplifying SEM for the masses while maintaining functionality
Scrapping the vacuum gage demonstrates the strategy Semplor used when designing the NANOS: If it’s not there, it can’t break or take up space. This enabled the design team to reduce the size of the SEM while also improving on its reliability.
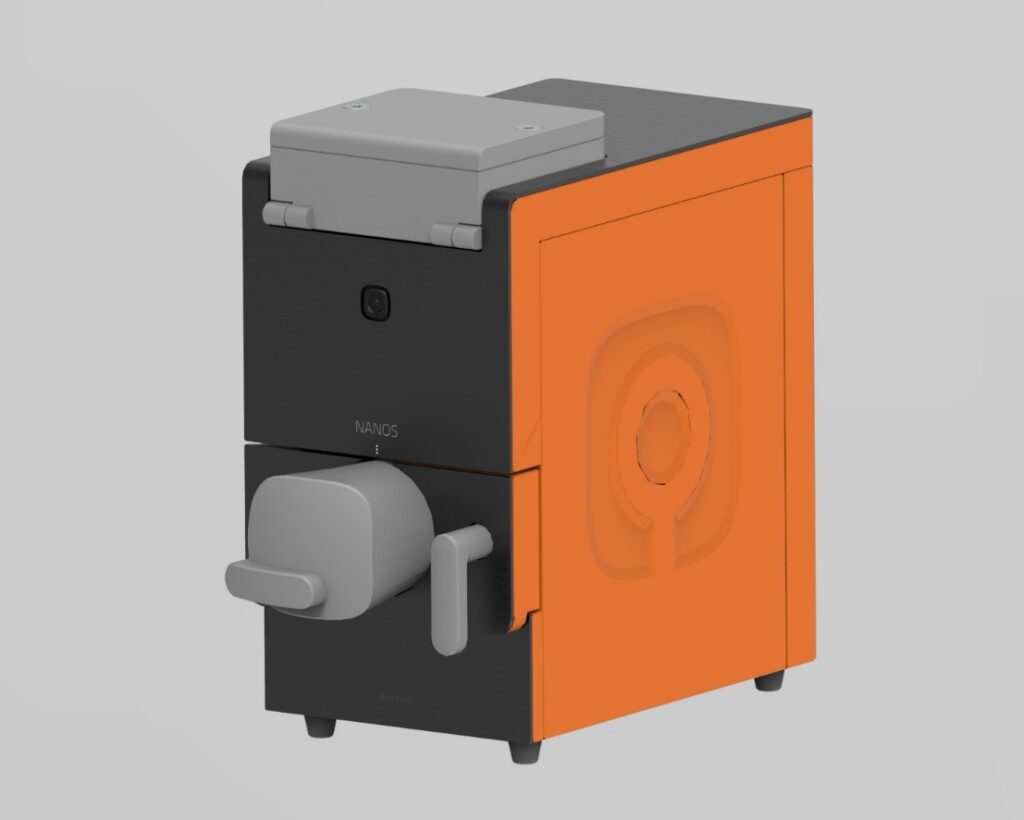
This philosophy, Asselbergs explains sets the NANOS apart from other tabletop SEM devices. “They are basically low-end systems and look like a large microscope shrunk into a smaller one. They are very traditional when you open them up.”
He admits that some aspects of the NANOS are similar to other SEMs. “Some things are physics, you can’t change that. But [the NANOS has] all new systems with today’s technology. All software and electronics are from the last three years.”
Asselbergs team produced many calculations and design permutations, early in development, to optimize the NANOS. For instance, a material might be well accepted by other SEM manufacturers for a given application, but Semplor asked: would another lighter, smaller or less expensive one work just as well?
This process of testing the assumptions of the SEM industry was then applied to all other aspects of the NANOS. Could it get comparable magnifications with fewer lenses? Can an off-the-shelf camera be used to navigate a sample? Could the number of cable connections be reduced by using one PCB to control the whole system?
“The mechanics are completely redesigned,” says Asselbergs. “The electro column is assembled more like the engine of a car [than traditional SEM]. It’s not stapled cylinder segments. It’s much simpler and works beautifully.”
Simplifying the traditional SEM design doesn’t mean the NANOS is short on advanced features and capabilities. In fact, it is the opposite, and the redesign enabled Semplor to develop new features and future proof the final product.
For instance, the NANOS contains an eucentric stage that keeps the sample in focus as its tilted. Thanks to this stage every sensor currently aimed at the sample will remain aligned and focused; all that changes as the sample tilts is the spot they are pointed to. In more traditional equipment, tilting the sample would require the user to change SEM settings to refocus the sample.
As for future proofing the NANOS design, Asselbergs says, “We designed a system that has a lot of space in the column to add more sensors that can aim at the same focal point as the other sensors and equipment. So, we can make it a more high-end system. You need to design for the future from the start.”
The role of engineering software in designing the NANOS
The main design team on the NANOS consisted of one physicist and one mechanical engineer. However, these individuals were far from alone when developing the equipment. They received help from Siemens, Enginia and even Semplor’s manufacturing partners.
“The system was designed and engineered with the people that would manufacture the system,” says Asselbergs. “We knew what they had in terms of manufacturing machines and based on that knowledge we designed the system for them to manufacture and assemble.”
Solid Edge was used to track the design, manufacturing and building logistics. This ensured all stakeholders, internal and external, were aligned. “We do nothing on paper,” says Asselbergs. “You talk to many suppliers and can have a meeting five minutes long without being in the same physical spot. Many suppliers have CAM systems to operate machine millings and lathes and it’s been my goal to work with those suppliers without making 2D drawings with tolerances.”
The 3D models made in Solid Edge also helped Semplor ensure that the NANOS was easy to maintain. For instance, designers were able to ensure that parts could be easily accessed and changed out. “It helps if you have a good 3D model of your system to assess if parts are easily accessible,” says Asselbergs. “We knew the system before we built it. If a PCB breaks, users untighten four bolts and a few connectors, put in the new PCB and send the old one in for a refund. You can replay this maintenance in Solid Edge to make sure it works, is easy and is optimized.”
Solid Edge didn’t just simplify the maintenance, logistics, prototyping and manufacturing of the NANOS, it also reduced the number of physical prototypes needed via simulations. Part stiffness, modal vibrations and other mechanical assessments were done using Solid Edge. Meanwhile, many of the field calculations and electron beam simulations were made using a separate academic software.
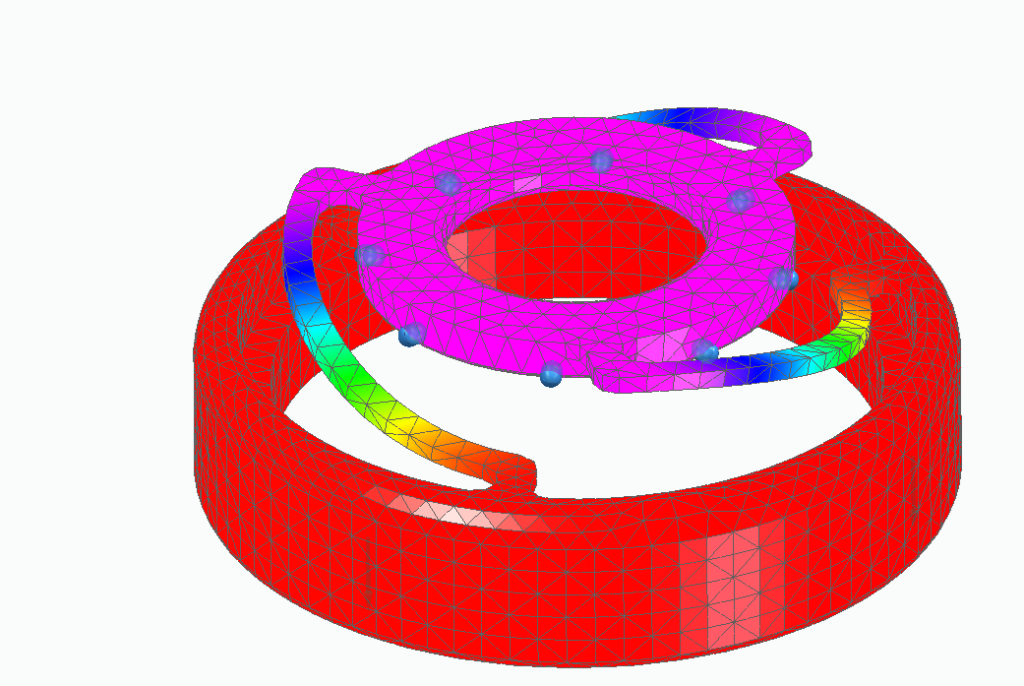
“A lot of simulations were done before parts were made,” says Asselbergs. “We looked at 10 different setups to optimize the design.” Regarding Solid Edge, Siemens and Enginia specifically, Asselbergs adds, “they helped us design the system to work on the first go. We’re very happy with it.”
This partnership is bound to continue. Since Semplor’s SEM design is designed to handle more sensors, it will need to optimize those setups as they are developed. What future capabilities the NANOS will have is a mystery — for now. But no doubt the work to design it will continue within Solid Edge and with the help of Siemens and Engina.
To learn how Solid Edge can help the development of your product, visit Siemens.