The family-owned furnace maker came from humble beginnings to become a leader in Italy’s push for industrial digitalization.
Siemens has sponsored this post.
One of the biggest challenges faced by legacy industrial companies is the transition into a digital age. Effectively digitizing your products and business can be a big hurdle, especially for small- and medium-sized businesses.
But Italian industrial furnace company Gadda Group has done just that, taking their more than 45-year-old family business into a more digitized world. Key to that transition has been the company’s use of Siemens’ Solid Edge and Teamcenter software mixed with an Industry 4.0 approach.
From garage to factory
Founded in 1978 by Rocco Vincenzo Adorisio, Gadda Group—which is still a family-owned business—has been producing industrial furnaces for more than 45 years. It had a humble beginning.
“My father started in a garage to produce furnaces,” Rocco’s son Stefano Adorisio told Engineering.com. “In 2010, me and my two brothers joined the company. Since then, we have grown a lot and guided the company into the digital era.”
Stefano is now an owner, proposal engineer and project manager at Gadda. He works alongside his brother Andrea Adorisio, a production manager, and his brother Simone Adorisio, general manager. They are continuing their family legacy of designing, manufacturing and installing industrial furnaces, while also making sure their products remain cutting edge. Gadda also manufactures many pieces of equipment needed to support a furnace operation, including automatic loading machines and quenching tanks.
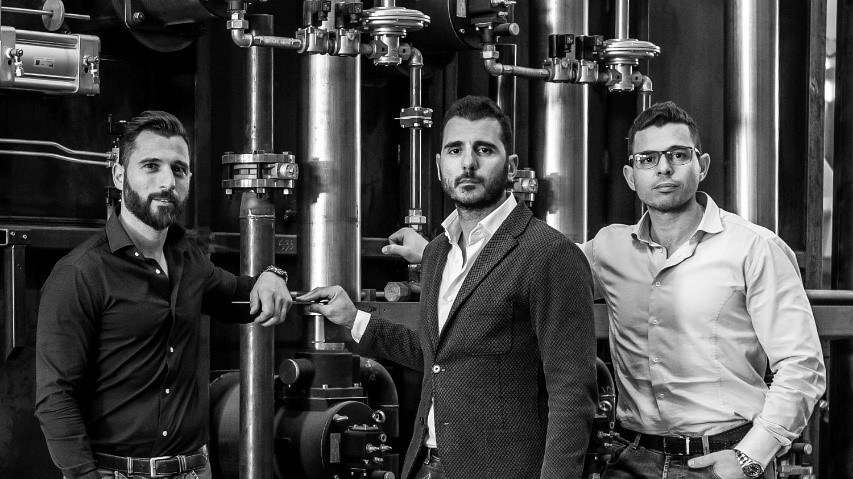
Today Gadda has 50 employees, including engineers, production workmen and technical support, with more than 6,000 square meters of production area in the Italian provinces of Turin and Milan. The company has completed more than 600 projects for more than 400 companies in over 20 countries.
Making custom furnaces with Solid Edge
Gadda does not take on a large number of projects, typically only producing around 30 units a year.
“We do not have a catalog. We have only references. So, every piece of equipment is tailor made for every single customer,” Stefano Adorisio says.
Gadda’s furnaces can heat parts up to 1,300° C inside of variously sized chambers, each designed specifically for a customer’s needs. The company’s clients represent a variety of industries including aerospace, automotive, and oil and gas, all needing to heat treat materials ranging from steel to titanium alloy.
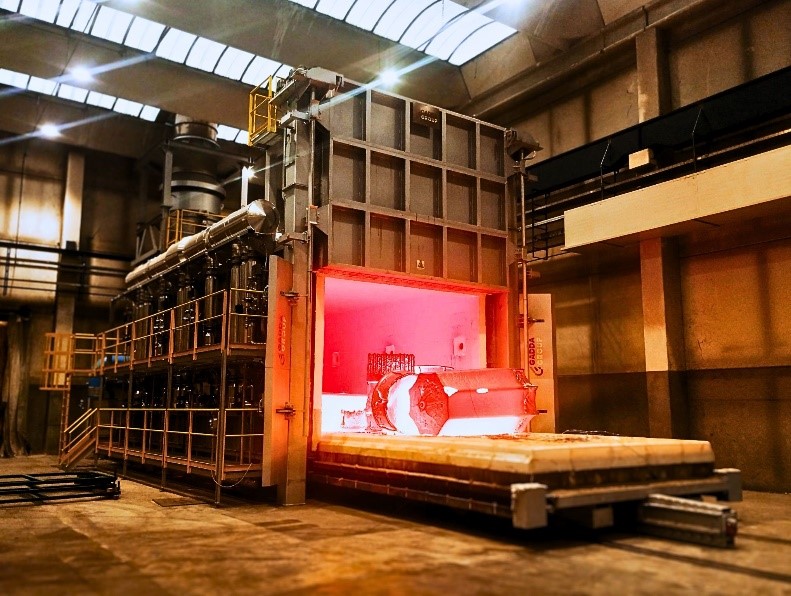
Two of Gadda’s custom furnaces have already debuted this year for Italian customers. The Bogie Hearth Furnaces will be used for heating large ingots up to 1,300° C and for forging. The larger of the two furnaces includes a 450-ton capacity and 11 pairs of flat flame regenerative burners. Gadda focused on ease of maintenance and safety in these designs.
Customization for each client requires a high level of design work, which for Gadda takes place in Siemens’ Solid Edge CAD software. Adorisio says that typically half of each project is constructed from standard parts and designs from other projects, while the other half is tailor made for each customer. It typically takes Gadda around one year to complete a furnace from when the order is placed to when the furnace is commissioned.
Adopting Solid Edge as the company’s design software has enabled the business to scale while taking this custom design approach. Gadda first explored using Solid Edge back in 2000 when a young engineer recommended that the organization purchase a single license of the software.
Gadda never looked back. Today the company has ten licenses of Solid Edge thanks to its partnership with Italian Siemens reseller Novasystem. All of Gadda’s complex, custom industrial furnace models now come to life in Solid Edge. The engineering team relies on simulation tools within Solid Edge, as well as the XpresRoute tool to simplify the piping and routing design process.
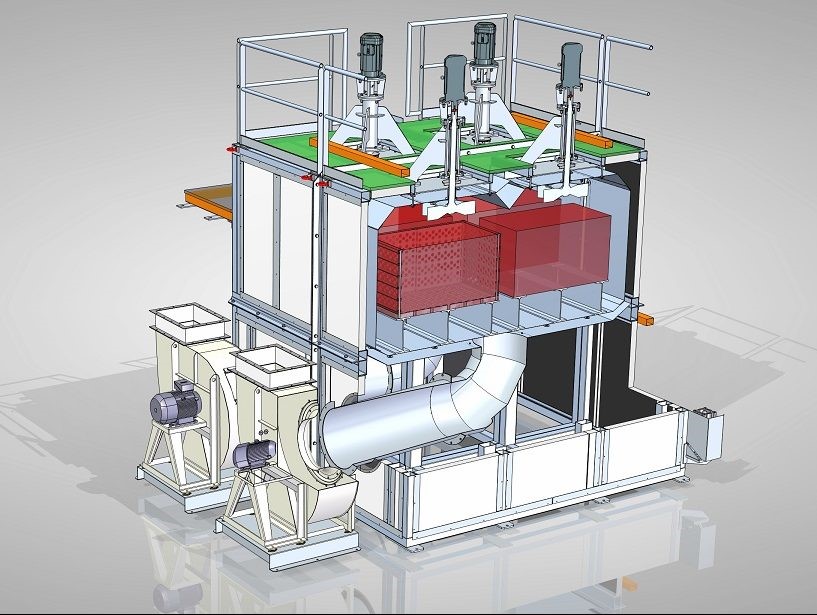
Gadda also adopted Siemens’ product lifecycle management (PLM) software, Teamcenter, after encountering issues with their previous system of design management.
“When two to three people were working on the same project, it was difficult to define who would do some parts and who would do other parts,” Adorisio recalls.
The company switched to Teamcenter in 2019 and saw immediate improvements. This software helped elevate the Gadda team’s collaboration and was an important asset for Gadda during the COVID-19 pandemic, when many of their employees worked remotely.
“With Teamcenter, it is very easy because of their system to check in and check out parts,” Adorisio says. “Everyone knows who is making some modifications to the project, and it also is easy to work at home.”
Firing up Industry 4.0
Being part of the business for decades, Gadda has continued to innovate, pushing their designs to ensure their products fit in with the evolving Industry 4.0 world and the modern smart factory.
“Industry 4.0 has become a standard for us because every customer today needs good automatization and a robust system to communicate with the equipment,” Adorisio says.

Gadda has incorporated many sensors into their industrial furnaces that can assist with predictive maintenance and improve safety, especially in their automated systems. Automation is even helping to reduce human error and safety risks for operators, who now play a more supervisory role, with things like heat-treatment recipes able to be programmed into the system remotely.
“I think that new sensors, new PLCs and new communication can help our equipment to reach higher performance in terms of efficiency and in terms of productivity. This was a step made together with all stakeholders: our customer, our supplier and ourselves,” Adorisio says.
The Italian government has also been a driving factor in pushing companies towards the Industry 4.0 approach and beyond. Italy launched Industria 4.0 in 2016, a national strategy for digitizing industry and encouraging new investment from domestic and international organizations.
Now, Italy and Gadda are both looking at the next step beyond Industry 4.0 and what it means for the country and company.
“In Italy, we are speaking about Industry 5.0, which includes artificial intelligence,” Adorisio explains. “I think that in the next five years, some of that new technology will also be part for our equipment.”
Thanks to modern design software and tools, this family-owned business plans to evolve and stay at the cutting edge of their industry.
Want to learn more about how you can adopt Solid Edge and Teamcenter in your business? Visit the Siemens website here.