The gap between information technology and operational technology is closing, and the increased interconnectivity is essential to Industry 4.0 and Industrial Internet of Things (IIoT) technology.
RS has submitted this post.
Written by: Gary Guess, Product Portfolio Manager at RS
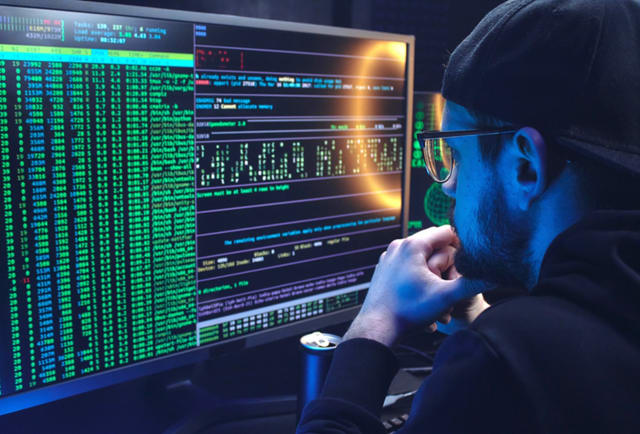
Traditional differences between IT and OT are quickly disappearing, enabling the increased interconnectivity essential to Industry 4.0 and IIoT applications, such as smart factories, warehouses, buildings and energy grids. IT/OT convergence allows facility managers to collect, manipulate and analyze OT system data to generate IT insights that can streamline operations, increase efficiencies, foster innovation and introduce new services. IT/OT convergence also allows facility managers to use IT system data to update and optimize OT systems so they can perform their physical operations more efficiently.
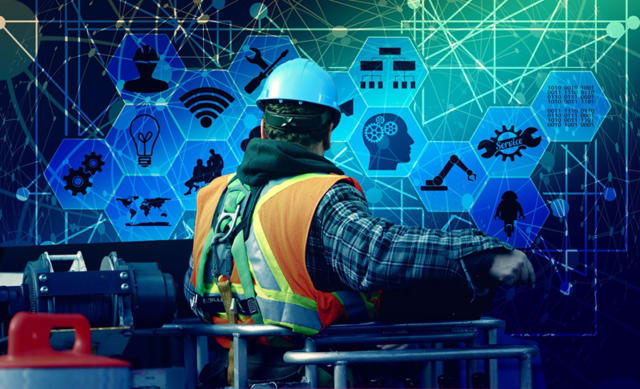
IIoT infrastructure — including Edge devices, wireless networks, cloud application programming interfaces (APIs) and distributed applications responsible for collecting, transmitting and processing IT and OT system data — is critical for any IT/OT convergence strategy. Edge devices collect data from industrial equipment to filter, prioritize and process OT data. Wireless networks send this data to the cloud, and then cloud APIs integrate this data into cloud-based IT systems. Although distributed IIoT applications are built on cloud IoT platforms, they run on both Edge devices and in the cloud to communicate and coordinate with IIoT infrastructure in real-time and tell IT and OT systems when and how to collect, transmit and process system data.
IT/OT convergence is revolutionizing applications including real-time remote asset tracking, monitoring and troubleshooting, predictive maintenance and equipment-as-a-service (EaaS). In the former, IT/OT convergence allows operators to see where a specific asset is located and when it will arrive at its destination. It also allows them to find out what a particular asset is doing and affects its operation.
In predictive maintenance applications designed for IT/OT convergence, operators can collect data to determine when an asset is likely to require maintenance and then schedule that maintenance to avoid unplanned downtime and reduce costs. IT/OT convergence in EaaS applications allows original equipment manufacturers (OEMs) to offer customers a usage-based payment structure so they don’t have to purchase assets outright. This approach saves customers from high upfront equipment costs and provides OEMs with predictable long-term revenue streams.
Information technology (IT) generates, collects, stores, manipulates, analyzes and delivers data within and between organizations via computing, networking and storage technologies. IT is characterized by the ability to be programmed and reprogrammed to meet the needs of various users, applications and networks and includes both hardware and software solutions. Examples of IT hardware include computers and networking equipment, such as switches, servers, routers, firewalls, storage arrays and backup devices. IT software examples can include programs like spreadsheets and databases, as well as operating, business intelligence (BI), enterprise resource planning, customer relationship management and manufacturing execution systems.
Operational technology (OT) monitors, processes and relays information about and controls physical processes in industrial workflows via computing, networking and storage technologies. Like IT, OT also includes hardware and software solutions. However, unlike IT, which is more flexible and programmable, OT is often designed to perform a specific task, such as monitoring mechanical performance, controlling heat or triggering emergency shutoffs. OT examples extend from simple applications like location tracking sensors to more complex applications, including programmable logic controllers (PLCs) and distributed control, computer numerical control, industrial control and building automation systems. For instance, OT can control the amount of electricity stored in a battery, the amount of liquid pumped through a pumping system and the HVAC fan speed. The supervisory control and data acquisition (SCADA) systems used to collect and evaluate industrial equipment data, optimize operational efficiency and minimize downtime are mere examples of OT in complex industrial control systems.
IT vs. OT
The key difference between IT and OT is how the technology is used. While IT is primarily used to collect and analyze information to raise awareness or regulate business processes, OT is primarily used to collect and employ information to control physical equipment processes. Additionally, IT can generally perform essential operations within programmed functions without much human involvement, while OT usually requires manual operation, like pressing a button, pulling a lever or flipping a switch. IT has also been most closely associated with white-collar work environments, like offices, while OT has generally been associated with blue-collar work environments, like industrial facilities.
Another key difference between IT and OT is that cybersecurity threats are relatively new to OT. Both sectors have long shared challenges including interoperability and equipment maintenance. But due to the closed nature of most OT systems, OT purchasers, operators and installers didn’t have to deal with many cybersecurity threats until IIoT technologies brought more physical systems online.
Although IT and OT are similar in many ways, they developed from different sources and weren’t designed to integrate. IT evolved from early file servers, PCs and mainframe computers, while OT evolved from the first digital control technologies designed to be integrated into machinery, such as PLCs. These divergent origins are at the root of their differences, but their unique combination of similarities and differences is what’s enabling their convergence.
As IT and OT have evolved to capitalize on more powerful computing capabilities, improved storage systems, superior networking technologies and new IIoT, artificial intelligence (AI) and machine learning technologies, they have also started to converge. Industrial systems designed for IT/OT convergence share data between IT and OT technologies to apply IT’s intelligence to OT’s physical assets and achieve new efficiencies. For example, temperature controls installed in OT have historically delivered closed-loop reports that had to be read on the factory floor. But IoT-enabled temperature sensors installed in OT can communicate with other physical assets to leverage the sum of their data and make precise, automatic adjustments in real-time to maximize performance.
IT/OT Convergence Benefits
IT/OT convergence is becoming increasingly mainstream, thanks to the evolution of powerful networking technologies, storage systems and computing capabilities, as well as the proliferation of IoT, IIoT, AI and machine learning technologies and the rise of Industry 4.0. Although many companies are still in the early stages of IIoT implementation and IT/OT convergence, the benefits are already evident.
The biggest benefits of IT/OT convergence include optimizing processes, mitigating machine downtime and maintenance costs, generating new service offerings and revenue streams and encouraging innovation. The combination of IIoT technologies and IT/OT convergence strategies increases efficiencies and streamlines, automates and optimizes business and physical processes. By collecting OT data about a motor’s energy use, for example, an IT system can regulate the motor’s operation to boost energy efficiency. Operators can also use IIoT devices to collect OT data and IT systems to analyze that data to develop predictive maintenance strategies that drastically reduce downtime and maintenance costs. IT/OT convergence also allows OEMs to shift from selling equipment to selling EaaS, eliminating high upfront equipment costs for customers. In addition, EaaS products equipped with IT/OT convergence systems can provide OEMs with valuable insights into customer use, encouraging innovations that can improve their value proposition and bottom line.
IT/OT Convergence Challenges
As mentioned, IT and OT purchasers, installers and operators have long faced challenges including interoperability and equipment maintenance. Cybersecurity has also been a longstanding challenge for IT and, now that more physical OT assets are being connected to the internet through IIoT devices, cybersecurity is a growing challenge for OT as well. Most IIoT devices are always online, providing 24/7 access to multiple points of entry. Because of this increased risk, chief information officers (CIOs), chief information security officers (CISOs) and IT departments in organizations around the world are working together to design systems and networks that provide robust, effective protection for every connection in both IT and OT systems.

Other IT/OT convergence challenges can include connectivity issues, data collection problems, cloud integration complications and application scaling and updating issues. For example, since OT often uses different communications protocols than Edge devices, using IT Edge devices to collect data from OT systems can be challenging. Some installers also find it difficult to connect Edge devices to secure wireless networks and to optimize those connections for energy efficiency and data transfer. Other common challenges include developing or sourcing the APIs needed to integrate OT data in cloud-based IT systems, scaling local or proof-of-concept IIoT applications to include new assets or locations, and keeping IIoT applications updated as operation demands evolve.
What these challenges all have in common is the complexity involved in purchasing, building and maintaining the robust IIoT infrastructure required for IT/OT convergence. To get it right, companies should seek input from experts in the embedded device firmware, wireless connectivity, IT/OT convergence security and cloud application development industries.
For more expert advice, visit us.rs-online.com/expert.