Cadmatic and CONTACT Software announce shipbuilding-specific PLM solutions.
The naval shipbuilding industry is a complex sector that encompasses several sub-sectors, including multiple marine and offshore solutions. The industry involves the engineering and manufacturing of various naval product types ranging from military frigates, commercial workboats, luxury yachts, purpose-built vessels and other naval equipment for maintenance, building and more. Furthermore, the shipbuilding industry expands to include associated services in related sectors such as transport, travel, entertainment, security, energy, research and the environment.
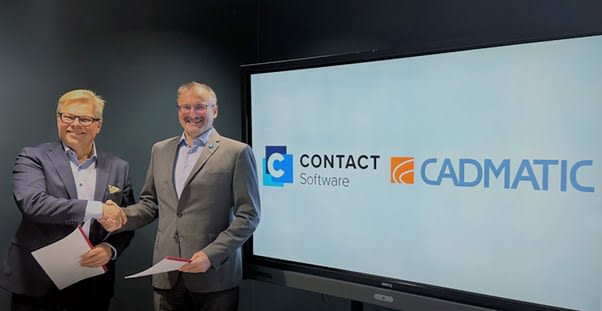
There is significant potential for digitalization in this industry, which would improve collaboration between contractors and shipyards, as well as help manage the large amount of technical and commercial data involved in the shipbuilding process. PLM and engineering simulation solutions can contribute to this digitalization effort by allowing for more effective data management and facilitating ongoing functional integration and change management across the design office and shipyard.
In January 2023, Cadmatic and CONTACT announced that they will collaborate to drive new opportunities for PLM process integration specific to the shipbuilding industry. Building on from this partnership announcement, I discuss the role PLM and simulation play to drive innovation in shipbuilding and improve the efficiency of the design and manufacturing process.
The State of the Shipbuilding Industry
Shipbuilding technology is rapidly transforming and consistently goes through changes. To understand those changes, one must understand what makes the shipbuilding industry unique and complex:
- Scale and complexity of vessels: Ships are often massive and complex structures, with intricate mechanical, electrical and hydraulic systems. These systems include an increasing amount of software and IoT technology. Therefore, the design, engineering and manufacturing processes for such vessels are highly specialized and require significant expertise in multiple disciplines.
- Regulatory environment: The shipbuilding industry is subject to a complex and evolving regulatory environment, with numerous international and national rules and standards that must be met. This includes safety, environmental and labor regulations, among others.
- Long project timelines: Shipbuilding projects are often multi-year efforts, with long timelines that require effective project management to ensure successful outcomes. These timelines also increase the likelihood of changes to regulations, technologies and customer requirements affecting the lifecycle of the project.
- Global supply chain: Shipbuilding projects require a global supply chain, with multiple suppliers and contractors involved in the design, engineering and manufacturing process. Managing the logistics of the supply chain, sourcing materials and components, coordinating with suppliers and contractors, and ensuring quality control can all present significant challenges.
- Variability in vessel types: The shipbuilding industry produces a wide range of vessels, each with unique design and engineering requirements. From commercial workboats to military vessels, each vessel type requires specialized expertise and technology.
Successfully navigating these complexities requires specialized expertise, technology and effective project management—most of which is supported by digital enterprise platforms.
“Shipbuilding is a unique industry with unique needs and levels of complexity,” agreed Cadmatic CEO Jukka Rantala in a release. “Our PLM and digitalization solution will come with in-built shipbuilding intelligence with the facilitation of data use and management to effectively support the lifecycle of complex engineering systems at shipyards. It will reduce the need for consultancy and implementation services that are typically required for general PLM applications on the market.”
The Benefits of Digitalization in Shipbuilding
CAD and CAE have been traditionally used in the design and engineering phases of shipbuilding projects. CAD software allows designers to create detailed 2D or 3D models of ships or other maritime equipment, while CAE software, aka simulation software, helps engineers to analyze and test the structural and mechanical performance of those models. The role of CAD and CAE has expanded beyond traditional design and engineering phases, now informing shipbuilding project planning and supply chain operational requirements.
For example, CAD models can be used to generate accurate and detailed bills of materials (BOMs), which can be used to inform procurement decisions and supply chain planning. By having a clear and detailed understanding of the components required for a vessel or other maritime equipment, supply chain managers can optimize their procurement processes, reducing lead times and minimizing the risk of delays or cost overruns due to unforeseen changes.
CAE also plays a role in supply chain optimization by providing insights into the structural and mechanical performance of components and subsystems. This can include hull simulations for space allocation, mechanical structure design and manufacturing, equipment parts, accommodation design and other engineering activities covering piping, HVAC, support, electrical, production and more. By running simulations and analyses on various design options, engineers can identify the most efficient and cost-effective components to use in equipment or on a vessel, drive open innovation and improve collaboration between contractors and shipyards. It can also help manage ongoing functional integration and change across the design office and shipyard.
Through the partnership with CONTACT Software, Cadmatic says in another press release that it aims at enhancing its design and simulation scope to cover “the entire lifecycle of shipbuilding projects—from design and engineering to prefabrication and production, and even to maintenance and operation.” Furthermore, the press release said that “Cadmatic will expand its offering to include the first shipbuilding-specific PLM solution that enables customers to significantly improve quality and save time throughout the lifecycle of shipbuilding projects..”
PLM and Simulation in Shipbuilding
PLM and simulation solutions have been used to improve ship design and performance, reduce material waste and optimize manufacturing processes. The Cadmatic and CONTACT partnership seems to be moving in this direction, as well. It also highlights the potential opportunities for PLM integration in the shipbuilding industry, particularly in areas such as ship design, production planning and performance management.
A few examples that underpin the value from such an integrated solution include:
- Data management processes
- Model-based systems engineering (MBSE) and planning
- Design reuse
- Product configuration
- Data classification
- Supplier collaboration
- Routing and automated workflows
- Product costing
- Service and maintenance management
Many of such examples are detailed in a report entitled Road to Shipyard 4.0 published by ECOPRODIGI Project and funded by the European Regional Development Fund in 2020, some of which can be summarized as follows:
- Multiple sources of data in shipbuilding projects can lead to confusion and errors. In shipbuilding projects, data is often generated and stored in multiple systems, including CAE, CAD, CAM and PDM systems. This can lead to confusion and errors, as different systems may contain conflicting or incomplete information. By establishing a single source of truth for all ship data, an integrated PLM ecosystem can help to eliminate these issues.
- Linking CAE, CAD, CAM and PDM systems can improve organization and management. By linking these systems together, data continuity can provide a comprehensive view of ship data, making it easier to organize, manage and leverage AI, AR and VR technologies. This can improve project planning, reduce errors and redundancies and improve overall efficiency.
- Contextualizing ship data can improve decision-making. By providing a complete and contextualized view of ship data, integrated data management processes can help stakeholders make more informed decisions. This can include decisions related to design, engineering, procurement and logistics, among others.
- Increased digitization can lead to improved performance. By increasing the level of digitization in shipbuilding projects, PLM and IoT solutions can help to streamline processes, reduce errors and redundancies and improve overall performance. This can lead to cost savings, improved project outcomes and increased customer satisfaction.
Digitalization includes leveraging 3D scanning, 3D printing, automation, warehouse automation and Digital Twins to increase virtual shipyard inspection. The shipbuilding industry is constantly evolving, and digital tools such as PLM technology and simulation systems are becoming increasingly important for driving innovation and efficiency. These tools can help shipbuilders reduce costs, improve design, increase performance and stay competitive.
To that extent, one release notes that “CONTACT Elements apps will be integrated with Cadmatic’s design, engineering and information management solutions portfolio to comprehensively address shipbuilding-specific digitalization needs and to optimize future shipbuilding-dedicated business, engineering and development processes in this challenging domain.”
The partnership between CONTACT and Cadmatic is said to combine two leading experts in the field, whose products and industry experience complement each other. According to Karl Heinz Zachries, CONTACT Software CEO, “shipbuilding companies worldwide will benefit from future-proof solutions to drive their digital transformation, meet growing market and customer demands and integrate sustainability into their value creation.”
Looking ahead, it will be interesting to learn more about the joint CONTACT and Cadmatic capability development roadmap, including how they plan to integrate their respective product portfolios, as well as with other critical platforms across the wider PLM, ERP and MES ecosystems.