Connectivity is a growing trend in manufacturing, and when done correctly it can be the difference between sustainable growth and spinning your wheels.
PTC has sponsored this post.
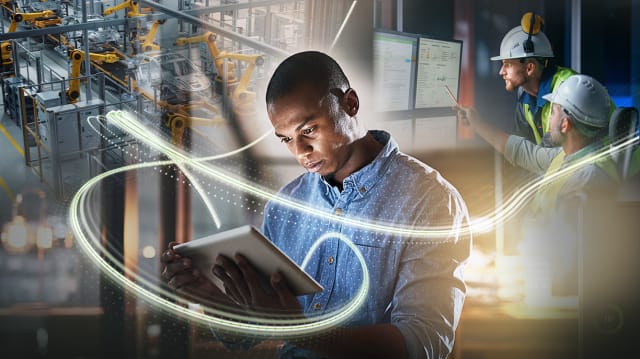
There are a lot of buzzwords used in the manufacturing sector to describe and promote the need for increased efficiency. From the early days of lean manufacturing and continuous improvement to digitization, digitalization and the current holy grail of digital transformation, all of these terms describe steps in the process of finding opportunities to reduce costs and improve margins from a machine, a manufacturing cell or an entire enterprise.
Another element all of these terms share is they rely on gathering and interpreting data generated by your equipment and processes to decide what projects to take on and measure the results. And while these terms describe actions that require data, how that data is captured and analyzed changes depending on your company’s technology, strategy and software.
If your company was starting its lean manufacturing journey 20 years ago, there’s a good chance you were encouraged to conduct a Gemba Walk, which means to gather your engineers and company decision makers and literally walk through the portion of the factory you were planning to improve. It’s a way for leadership and the people tasked with implementing change to get first-hand observations of how a process works and where the pain points are. It’s a basic and completely analog method of information gathering, but is an effective and experiential way to visualize the changes that must be made for a company to find internal efficiencies.
Even today, an old-school Gemba Walk can be a valuable tool for process improvement. But the manufacturing technology used in today’s factories now produces and gathers huge volumes of data, creating opportunities to find impactful process improvements that could never be identified by simple observation.
These types of improvements vary in scale from very granular—such as optimizing the amount of fluid used to cut parts in a CNC machine—to transformative, enterprise-wide changes that drive growth and competitive advantage. However, any company looking to extract this kind of value from their operations needs a process to gather and collate the data from hundreds or even thousands of individual sources in a useable way that makes it easy to manage, analyze and act upon.
Strategic Versus Tactical Connectivity
At its heart, enterprise connectivity is the ability to collect data from your machinery or industrial assets across all of your factories. Not just one line, not just one factory or distribution center, but across all of your assets globally.
Regardless of what your enterprise consists of, company-wide connectivity requires a layer of software that can speak to every asset in the company, new or old, and aggregate that data into one single source of truth for the organization.
“A lot of companies are at different points in their digital transformation or process improvement journeys. There are some companies still working out tactical kinks, like finding the correct driver or protocol to connect to the various types of equipment, or determining the type of data they want to collect,” says Kyle Carreau, sales enablement engineer at PTC, Kepware channel. “But if we’re looking at it from a strategic standpoint, you need a solution that is both centralized and decoupled—you need it to scale up effectively. Can this process be repeated? Can this technology be installed somewhere else in the plant? Can this be monitored?”
“But from a tactical level, you also need a solution that’s going to be able to handle the diverse assets of your company, whether that’s different devices, both legacy and modern, equipment from different vendors, or even just different types of assets that aren’t necessarily a PLC or motion controller,” says Carreau.
PTC’s Kepware is an example of the type of industrial connectivity solution that helps businesses connect automation equipment, and devices to software applications. The key is that solutions like Kepware combine hundreds of drivers and protocols in a single server, connect to automation equipment from a single interface, and then convert that industrial data into various types of protocols including OPC UA, MQTT and HTTP. It connects with any type of equipment from any OEM.
Connectivity from Old to New
When a manufacturing company buys a new machine, they’re optimally looking to get about 20 years of operation from that asset. The problem is that this doesn’t always play well with the current demand for data.
“Ideally, you are looking for a solution that can connect to both older equipment and newer equipment. By doing this, you are ensuring that data from your machines will always be available,” says Carreau.
In fact, he says that with the right connectivity solution you can build out a schedule for this sort of thing to maintain an older piece of equipment for an even longer period of time. If you have more information about a machine, you can start to very cleverly start planning out when potential parts may go down.
“If your PLC’s getting that data, you can extract that out from Kepware, and then you can compare in real time what that vibration analysis may look like. The importance of connectivity is you can now dig through the data and come to those conclusions. No solution can make those decisions for a company, but the right one can help enrich that data to make those decisions easier,” says Carreau.
Layering Connectivity
Implementing enterprise-wide connectivity should follow the ISA-95 model, meaning that different levels of assets require different types of connectivity. Starting at layer zero is the sensors on specific equipment. PLCs and SCADA systems make up the second layer. Layer three is the manufacturing execution system (MES) and layer four would be the enterprise resource planning (ERP) software, or something similar. Without a solution to translate and house data, to get sensor data up to your MES or higher, that data had to pass through all the different layers, like a staircase where you have to stop at every single floor. “It was a good solution for the time, but what ends up happening is that the data changes hands and errors can be introduced, meaning the data looks a lot different once it gets to that higher system than it did directly from the plant floor sensor or PLC,” says Carreau.
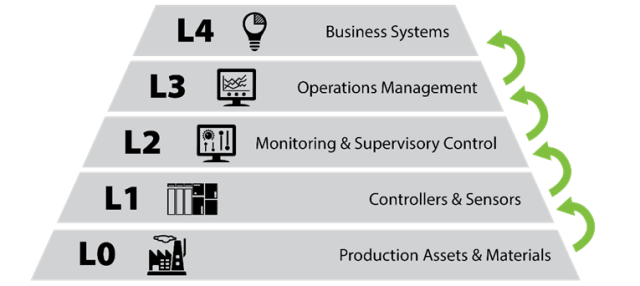
With solutions like Kepware, this data transfer is more like an elevator. The idea is that if you have a centralized data repository that can communicate shop floor-level data to higher level protocols, you can essentially skip floors.
“If I have production data from my PLC that needs to go all the way up to the ERP system, we can just send data directly there as opposed to hopping through all these hoops. It becomes a lot easier for that data to be shared throughout an organization,” he says.
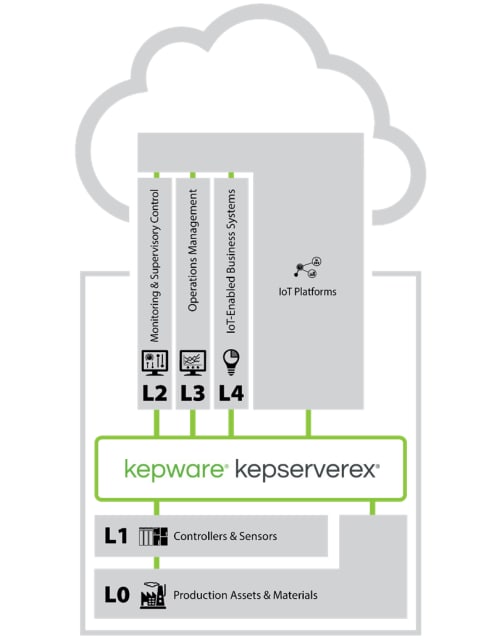
Connectivity Outcomes
If you solve the connectivity problem, every other aspect of digital transformation and continuous improvement becomes a lot simpler. Traditionally, connectivity has been an afterthought for capital equipment implementation projects—get everything installed and commissioned and then hook it up to the system. With a connectivity solution such as Kepware, companies are able to able to solve that issue before a piece of equipment even arrives.
“Getting people to start thinking about connectivity as an enterprise-wide strategy in order to help with implementation of either new equipment coming in, helping with efficiencies in monitoring overall equipment effectiveness (OEE), helping to improve quality and just getting access to that data in a very centralized, decoupled and secure way is an important step,” says Carreau.
Indeed, enterprise connectivity is a growing trend in manufacturing. When done correctly, it can be the difference between sustainable growth and an uncertain future.
Visit PTC to learn more about Kepware and enterprise connectivity.