Engineers need to deploy the correct problem solving techniques to arrive at the best solution and avoid repeat occurrences.
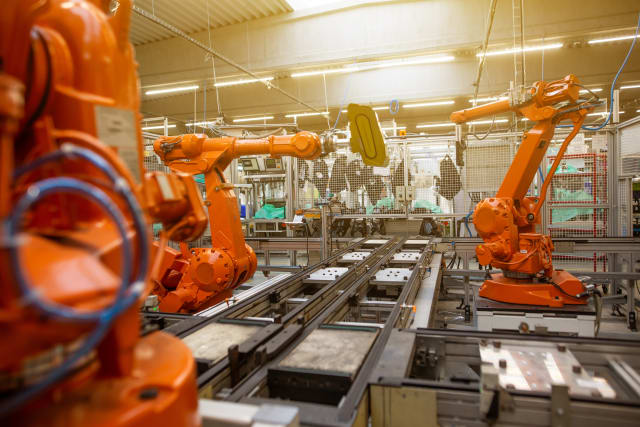
Let’s face it, manufacturing is complicated. Even the most advanced, well-managed factories will experience manufacturing problems on an ongoing basis. Some of these will be simple and have an obvious, quick solution while others will require rigorous exploration to uncover the root cause. One thing that shouldn’t change, however, is how engineers approach manufacturing, maintenance, design and shop floor problems.
It’s vital to consider all the potential causes and solutions before arriving at a conclusion. As data is collected and analyzed, initial solutions can inadvertently be favored over more correct options. Referred to as “confirmation bias”, this involves knowingly or unknowingly favoring information that supports preconceived ideas while ignoring or discrediting data that contradicts them. It’s a common and often subconscious tendency, which makes it extremely important for engineers to be aware of this bias.
Every effort must be made to consider the totality of perspectives, causes and solutions to arrive at the best outcome for a given problem while avoiding suboptimal results and continued or recurring malfunctions. The tendency to favor or fixate on one particular solution can only be overcome using solid problem-solving tools and methodology.
Various tools can be deployed depending on the nature of the problem, the desired outcome and the resources available. One example, the Red X process, helps avoid confirmation bias in a variety of ways. Red X, developed by Dorian Shainin, refers to the dominant root cause shown as a color-coded red on a chart that prioritizes what is observed to have the greatest effect on the quality of a process (also known as a Pareto chart).
This technique begins by recognizing a problem exists and must be solved. A trained, skilled facilitator can help guide and teach and many companies train key personal to lead the Red X process when problems arise. The focus should be on finding the root cause without the baggage of preconceived notions of what the problem or solution could be. The strength of this technique is that data is collected by testing a variety of hypothesis. The analysis of the data—using statistical tools—is used to identify patterns or trends that could, in turn, point towards a root cause. Multi-discipline teams are often used to provide multiple perspectives, forcing the team to keep an open mind throughout the process.
Another simple, popular method is the 5 Why’s method of problem solving. Engineers often identify the root by pushing themselves to continually ask “why?” This is methodically done in steps:
- Define the problem
- Ask why the problem occurred (this should generate a reason).
- Ask why the reason existed that caused the problem (this should generate a second reason).
- Ask why second reason was caused and discover yet another reason.
- Repeat this process at least 5 times or until the actual root cause and reasons are found and can be addressed.
Using the 5 whys helps avoid confirmation bias not only by challenging initial assumptions but by encouraging the problem-solving team to consider multiple potential causes. Continuing to ask “why” ensures the engineer looks deeper and considers alternative causes or factors that may not be obvious contributors to the problem. This approach ensures the root cause is identified which avoids just treating the symptoms of the problem.
Real-Life example
Let’s look at an actual industrial event from my career as an engineer to illustrate how bypassing data analysis can result in a repeat of the same catastrophic event. In this example, the second event occurred not long after the initial damage was repaired and new equipment replaced. It began when a transformer failure and subsequent fire shut down an entire vehicle engine plant as it was ramping up into production. The failure happened after protective relays tripped in succession all the way back to the main substation. After isolating the transformer and resetting the relays, the failure was quickly blamed on premature failure of the new transformer—most likely from a manufacturing defect—combined with a lack of fuse and relay co-ordinations by the contractor
The only action taken was to update the fuse and relay coordination to ensure only the defective transfer would be isolated if another event occurred. Shortly afterwards, a new transformer arrived and was put into service.
Looking closer at an overview of this sequence of events should have immediately raised red flags. Even the most basic data collection never took place. However, the engineers were surprised when, less than three months later, a second power transformer suffered the same fate although the new coordination settings prevented the entire plant from shutting down.
A new investigation revealed that the transformer insulation had been slowly degraded over time due improper transient suppression. The transients were created when switching events occurred around the industrial complex the plant was located near. Had an investigation team been commissioned after the initial failure, they would have discovered the identified causes were unlikely to have triggered the short and fire in the first place.
Confirmation bias happens all the time. An example in everyday life could be the transition to electric vehicles (EVs). Moving directly from one method of energy consumption to another seems to be the accepted approach. However, it can be argued that it is better to first focus on conserving energy before converting to EVs because it’s more effective and efficient to reduce energy consumption through conservation measures rather than simply replacing fossil fuels with electricity. This approach could offer a reduction in carbon emission while allowing more time to modify the global infrastructure to accommodate the conversion to electric. This example shows that often the conclusion is used to justify the solution instead of taking all the potential measures into account first. Also, jumping right to conversion bypasses more timely and beneficial steps that will now never be implemented.
Confirmation bias does not preclude the finding of solution, especially in situation where more than one solution exists. Also, having a bias does not mean your solution is not the correct one. However, using good problem-solving methodology is always the best way to approach any engineering challenge, whether in troubleshooting or design.