The vibration analysis inspection payload for Spot, Boston Dynamics’ mobile robot, turns every camera pixel into a sensor.
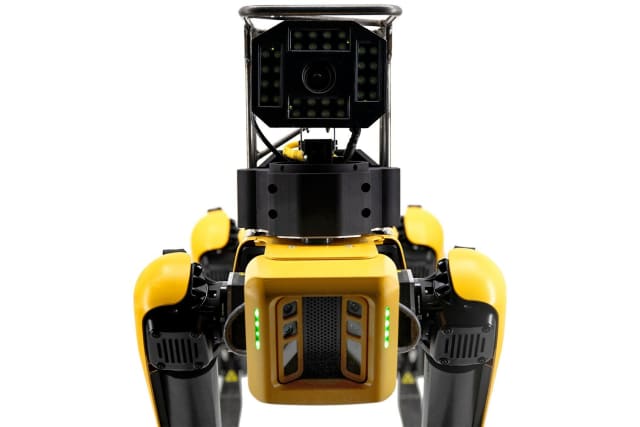
The camera-based Iris Explorer payload for Spot combines the mobility and automation of Boston Dynamics’ mobile robot with motion amplification vibration analysis technology developed by RDI Technologies, creating an autonomous solution for active condition monitoring in factories or remote and hazardous environments.
“Our integration with Boston Dynamics creates significant opportunities to transform asset-heavy industries,” says Jeff Hay, CEO of Knoxville, Tenn.-based RDI Technologies. “Vibration analysis is a high-value part of every asset maintenance program. In bringing together industry leading vibration analysis and robotics in RDI’s Iris Explorer Spot payload, we’re providing critical tools to address challenging business problems—increasing safety and productivity while improving operations and assets in complex industrial environments.”
The Iris Explorer payload is driven by RDI’s Motion Amplification technology. Measuring deflection, displacement, movement and vibration not visible to the human eye, the technology turns every pixel in the camera’s view into a sensor capable of measuring vibration or movement with high levels of accuracy. It provides instant visual imagery of hard-to-detect faults such as misalignment, bending, soft foot and separation, along with trending of vibration readings to monitor chronic or emerging issues.
Active condition monitoring is time-consuming, meticulous work; if rushed or done improperly, data has little value and entire routes must be redone. This is where Iris Explorer’s Automated Feature Finding capability comes in handy. It repeatedly captures the exact same image data every time, across every route, for every asset, in any environment, every time it heads out on the floor.
The Iris Explorer payload captures full field of view of an asset and captures conditional, automated data triggers. This means customers can focus on the most relevant data, without repeating routes—a common problem in asset maintenance.
Combined with Spot, route-based operations become seamlessly automated and remotely monitored. Customers apply the same observation protocols on the thousandth inspection as it was programmed to do on the first—without human error or bias—while controlling and performing routes remotely across plants.