Sustainable design is no longer a dream thanks to PLM integrating with environmental LCA.
Almost a decade ago I handed in my master’s thesis with a lot of hope, fear and pride. At the time, Environmental lifecycle assessment (LCA, sometimes E-LCA) was not widely used in an engineering setting. There was a chance, my professors told me, that the review board wouldn’t see the value behind it. But believing LCA could help engineers save the world, I wanted to spread the word. I passed but the professors were right, and one board member needed heavy convincing.
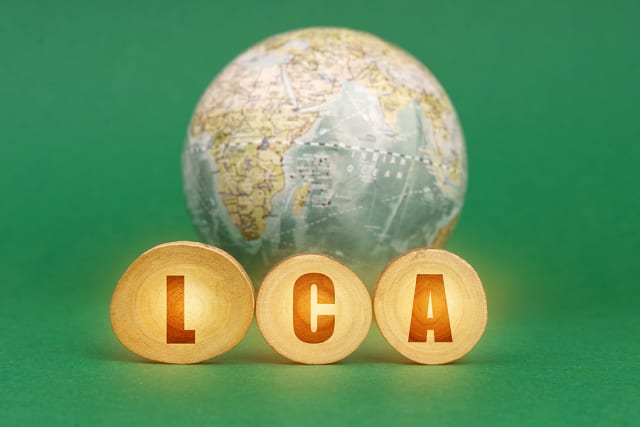
Ten years later and you can’t sneeze without seeing a company boasting about how their green objectives are improving sales, reducing energy and decreasing costs. Those that perform an LCA have the numbers to prove it. And these early adopters of LCA look to benefit even more in the wake of governments and international bodies implementing laws and agreements to reduce carbon emissions (including the Paris Agreement, EU’s new climate law and various country-specific spins on the Green New Deal). In short, going green is no longer a nice-to-have marketing or cost reduction tool—it’s a necessity. And slapping a green label on something—a marketing trend known as greenwashing—won’t cut it anymore; with the introduction of these laws, companies need the numbers to back up their claims.
In response to all this pressure towards environmentalism, the 2022 trend for PLM companies has been to integrate LCA tools into their technologies. This change has made producing environmental reports a trivial process—so trivial, in fact, that it can easily be added to any product development cycle.
Since “80 percent of the environmental footprint impacts are locked in during the design phase, it’s very important to bring LCA into the beginning of design to have a major impact on how sustainable a design can be,” says Muriel Moreau, CATIA Sustainability and Data Sciences Experiences Portfolio Director at Dassault Systèmes. “It is important to have LCA as a tool to define a path towards decarbonization and limiting all the impacts that a design can have on their environments.”
In other words, a key method for companies to meet their 2023 green objectives is to use PLM technology, coupled with LCA workflows. These workflows can be used to optimize products environmentally in a similar way to how an engineer would optimize a strength-to-weight ratio. So, let’s dig into these processes and how they can make 2023 the year PLM and LCA save the planet.
What is Lifecycle Assessment? And How Will PLM Help?
First, let’s define lifecycle assessment (LCA). It is a systematic process used to compute the environmental impacts associated with a product, or service, over its lifecycle. In other words, it’s a study of the environmental impacts caused by the things that engineers design—from initial ideations to end of life. Though the tool can’t define something as “sustainable” it can be used to compare environmental impacts of competing products and design iterations.
The process is generally made up of four stages:
1. Goals and Scope: Where the reason, aims, boundaries, functional unit (a normalizing factor) and environmental impacts are defined.
Here, engineers define the rules that govern the calculations. These rules outline, for example:
- What is in and out of scope for the assessment (easy to define thanks to PLM data).
- How the burden of environmental impacts is split between co-products.
- How environmental impacts will be split if activities affect multiple unrelated products (i.e., the transport of various small products in large shipping containers).
However, the most important decision in this section is the definition of a functional unit. Since the value is used to normalize results—so that comparisons can be made—choosing a bad functional unit will skew the numbers.
For example, when comparing environmental impacts of different food products, should the functional unit be one kilogram or 100 calories of food? The challenge with that question is that different foods have different caloric densities. Therefore, by comparing the environmental impacts of a kilogram of spinach to a kilogram of beef, the data will produce results that skew differently than when comparing the impacts of 100 calories of spinach and 100 calories of beef.
2. Inventory Analysis: Where all the direct emissions, material and energy flows within the system are collated into one database.
Traditionally, inventory analysis is the most time-consuming part of an LCA. It is where the engineers calculate all the materials, direct emissions and energy produced and consumed within the boundary of the defined system. Everything is collected in these calculations, from how much electricity the product consumes when in use, to how much steel went into the construction of its manufacturing plant. This makes it a monumental task.
The benefit of the digital twin and PLM is that much, if not all, of that information will already be accounted for during the design of the product. The only reason this was difficult in the past was because LCA was traditionally done by third parties after products were released. Since that early data wasn’t accessible to the third party—as they frequently had no access to design documents–they would often measure, estimate, research or consult industry averages for the data. This process takes time and can often yield questionable results.
3. Impact Assessment: Where environmental footprints are calculated.
During the impact assessment, all the information from the inventory analysis is fed into computations to assess the environmental impact of the overall process. These computations are generally based on data collected by industry and environmental agencies and then collated into libraries for LCA practitioners.
For instance, this database would have location-specific energy mixes and how those mixes translate into impacts such as greenhouse gas emissions and land use. The LCA practitioner can take the total amount of electricity used at each location, and each location’s energy mix, to estimate how much GHG emissions and land was used to produce all the electricity needed during the product’s lifecycle.
With the addition of LCA tools into PLM technologies, all the environmental impact data is at the fingertips of the engineer designing the product. In theory, by tweaking a design (by changing the size of a part, for instance) all the calculations can be done under-the-hood so that the impact values automatically update within the PLM system for each iteration.
4. Interpretation: Where data is presented, reviewed, compared, assessed, validated and sensitivity tested.
During the Interpretation stage of the LCA, the design engineer can begin to make informed decisions about the environmental impact of the product.
For instance, instead of the design engineer just assessing the strength of the design based on whether it’s made from steel or aluminum, the environmental impacts of those two designs can also be added into that assessment. The idea is to better inform the trade-off process using environmental data when selecting final designs.
“With the combination of the virtual twin and lifecycle assessment, we have precise scientific environmental computations that can be done very early in the design cycle,” says Moreau. “That will help our customers to do trade-offs and choose between technologies.”
Moreau continues to say that by putting LCA into the heart of the virtual twin, engineers will be able to perform faster assessments. These fast LCAs will then be a catalyst for design innovation from an environmental perspective.
Connecting LCA to PLM
So, how has LCA been embedded into PLM systems over the years? It should be noted that PTC was ahead of the curve and has featured embedded LCA technology in the Windchill workflow for over a decade now. Thus, PTC has a series of success stories proving the value of these types of tools.
However, in 2022 the trend started to really kick off. After the recent pressures for industry, governments and consumers to go green, Dassault Systèmes led the year’s rallying cries to connect LCA workflows into PLM tools with the release of Sustainable Innovation Intelligence.
“We really believe in putting LCA on top of the Virtual Twin,” says Xavier Adam, Sustainability Senior Manager, Dassault Systèmes. “Basically, we extended what we did for the aerospace and defense industry on their weight balance solution. It is critical in that industry to have the lowest weight possible but to also have good balance. The same mechanism is reused here for the environmental impact.”
Now that two PLM players had their toes in the LCA market, it isn’t surprising that late in 2022 Siemens Digital Industries Software followed suit and Makersite, an environmental tool, announced a similar process that could be integrated into an Autodesk workflow.
“It’s best that everyone does it,” says Jonathan Dutton, Sustainability Marketing Director at Dassault Systèmes. “Everyone should be doing this. If we want to collectively make certain that we are in a sustainable world and reducing carbon emissions, pollution and improving biodiversity … It is something that should be integrated everywhere in all equivalent [PLM] software. It should be something that’s integrated into the daily lives of all people who are involved in designing and developing the future products that will be put on the market.”
With LCA tools integrated into PLM and digital twin systems, much of the information needed to perform an LCA will already be baked into the design process. As a result, engineers can have a running tally of the environmental impact of their designs as they iterate towards a final, more sustainable product. The easier, faster and better embedded into the design process this becomes, the more likely engineers can use PLM and LCA to save the world.