Safety Awareness Bundle combines classroom with hands-on training to ensure that workers and robots can do their jobs safely.
As robots and robotic platforms become more prevalent in the workplace and factory floor, so has the need for the employees working alongside them to have the proper skills to interact with them safely.
Festo Didactic, a leading industrial and technical education provider with expertise in automation, has partnered with SICK, global manufacturer of sensors and safety systems for industrial applications, to respond to that need with a new training curriculum.
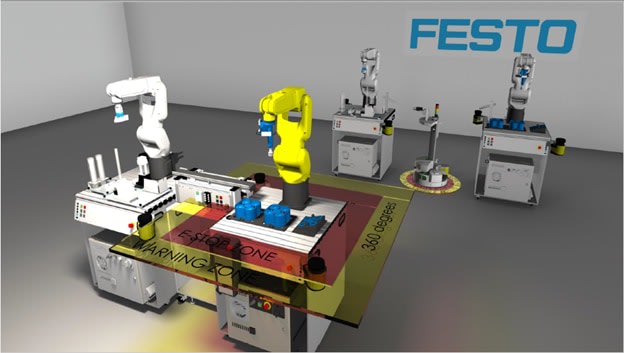
The Safety Awareness Bundle connects the training curriculum to real-world applications and hardware. Students learn robot risk assessments and how to implement a system approach as well as à la carte automation solutions. Students apply what they learn in the classroom to a Festo Didactic manufacturing production system, which features a simulated Cyber-Physical Smart Factory with a six-axis robot, SICK area scanners, safety programmable logic controllers and a safety relay.
Not only does the curriculum give students valuable classroom and hands-on training but it also shows them what to do with the digital data associated with risk assessment through training on the Six-Step Method of Robotics and Automation equipment safety. This method enables students to understand risk assessment, safe design, technical protective measures, overall machine validation, machinery deployment and administrative measures, and information about residual risks. Students also become familiar with terminology, such as performance measures, areas of severity, frequency and avoidance.
“With such a demand for smart manufacturing methods to be demystified, students who have been exposed to this sort of implementation have a real advantage when it comes to applying to jobs compared to students not provided the same experiential learning and job training,” said Ted Rozier, director of engineering at Festo Didactic North America.
Students will learn robotics safety concepts such as those used by SICK to create a safe and efficient palletizing operation.
Conventional robotics training tends to focus on specific robot brands and their operation. In contrast, Festo Didactic and SICK designed their curriculum to be robot agnostic and adaptable to a variety of leading robotics platforms. Festo has added the curriculum to its Manufacturing Production System and Cyber-Physical training equipment to help students learn real-world robotics integration systems.
The Safety Awareness Bundle has already been set up in several community colleges and universities in the U.S. In fact, in rolling the program out to education partners, Festo puts a priority on the robotics systems already in use in the partner’s community—and uses that to inform which brand of robot to recommend for the program. This way, the education partner can purchase the brand that will best support students’ chances of being hired locally—and enable them to be able to contribute immediately on the job. The program isn’t just useful for current students. Workers can also access the course to boost their skills and expand their knowledge of robotics.
“It’s imperative to have a workforce that’s adept to risk assessment in order to prevent and mitigate hazards,” said Rozier. “Protecting machinery and personnel against accidents—reducing liability, but not productivity—should be top of mind for everyone, including the robots.”
It’s no longer the case that robots perform only dirty, dull and dangerous work, where they are separated from human workers: robots and people now work side by side—and safety must be a top priority. Students who complete the training will gain skills that are in high demand in the modern work world and will be able to make careers out of ensuring that workers and robots work well—and safely—together.