Automakers are racing to develop this promising battery technology, and they’re nearing the finish line.
For years, solid-state batteries have been promising a significant shift in the electric vehicle (EV) industry. With more energy density than today’s lithium-ion batteries, solid-state batteries have the potential to double EV driving range while being safer and quicker to charge.
There are still important engineering challenges to solve, but full-scale commercialization of solid-state batteries is closer than you might think. Here are the latest developments in solid-state battery technology and the reasons to be optimistic about their future.
What is a solid-state EV battery?
Unlike the lithium-ion batteries that power today’s EVs, which use liquid electrolytes between their electrodes, solid-state batteries employ a solid electrolyte. This provides a higher energy density, meaning lighter and more efficient EVs with longer driving ranges.
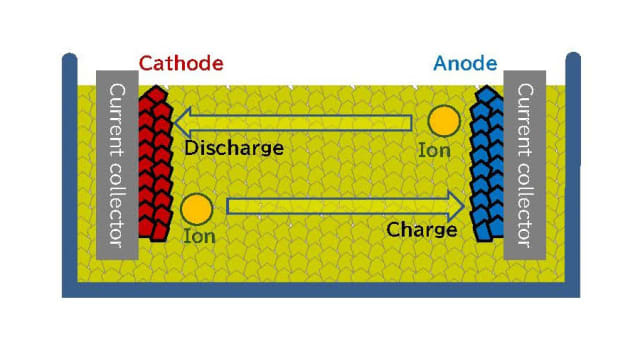
That’s not the only advantage of solid-state batteries. They’re safer and charge faster than current lithium-ion batteries, and they’re stable in the face of high voltages, high temperatures and temperature changes. It is no surprise that solid-state batteries are considered a technology of the future and will probably be the next big step in battery development.
However, there’s one big problem with today’s solid-state batteries: dendrites. These are protrusions that form on the anode surface during charging when lithium ions move from the cathode to the anode. The ions attach to the anode surface, creating a bumpy surface where dendrites can take root. During discharge, that coating is slowly stripped from the anode and creates tiny potholes. This results in even more uneven plating in the next charge. The dendrite’s structures rise like roots into the electrolyte and penetrate the barrier between the anode and cathode, causing cracks and a short circuit that could result in fire.
The latest research on solid-state batteries
In January 2024, researchers from the Harvard School of Engineering and Applied Sciences (SEAS) presented a solid-state battery with a lithium metal anode with an impressive charge/discharge cycle capability achieving 6,000 cycles, more than any other pouch battery cell on the market. The research and results were published in Nature Materials.
The researchers faced the familiar problem of dendrites forming on the anode’s surface. Initially, in 2021, they proposed a multi-layer battery design, applying materials with varying stabilities. Rather than preventing dendrite formation, this approach focused on controlling and comprising dendrite formation. In the more recent research, the team successfully prevented dendrite formation by incorporating micron-sized silicon particles into the anode, effectively obstructing the reaction with lithium. This strategy facilitated the uniform and homogeneous plating of a thick layer of lithium metal around the silicon core, creating a smooth surface that ensures an even current density distribution and prevents dendrite growth. With this improved design, the researchers say, the battery can be recharged in just 10 minutes.
Current market trends and future commercialization prospects
While numerous companies are actively involved in the development of solid-state batteries, Japanese enterprises have emerged as leaders in this field. In October 2023, Toyota and Idemitsu Kosan announced a partnership to develop solid-state batteries for EVs. The companies aim to establish a robust supply chain and mass produce commercial solid-state EV batteries as early as 2027.
Toyota and Idemitsu Kosan will focus on sulfide solid electrolytes, which they believe are promising for EVs due to their softness, flexibility and adherence to other materials that contributes to an efficient production process. Its crack resistance potential holds promise in solving a major challenge associated with solid-state batteries.
Honda is also seeking to transition from liquid to solid electrolytes, with the company recently suggesting that solid-state batteries may be a way to make EVs more affordable. To facilitate large-scale production of solid-state batteries, Honda is working on defining fabrication techniques and selecting optimal materials. The company is employing specialized stamping processing techniques to enhance the solid electrolyte density. Together with careful material selection, these efforts aim to improve the interface between electrodes and electrolytes, thereby providing a smoother flow of ions.
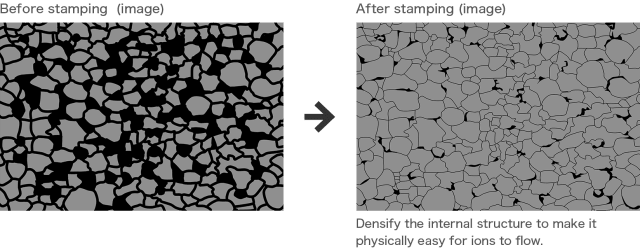
There are still many unknowns in solid-state battery manufacturing technologies, but Honda believes that their roll-pressing processing technique will enable high manufacturing productivity with high battery performance. The challenge is to establish optimal stamping pressure to avoid material microstructure damage and define how the electrolyte density affects battery performance.
It’s not just Japanese automakers that are pursuing solid-state EV batteries. U.S. company QuantumScape is collaborating with Volkswagen on a lithium metal architecture that incorporates a solid-state ceramic electrolyte with high dendrite resistance. Their separator is designed to resist dendrites even at extremely high current densities, facilitating fast charging. Their goal is to achieve a full charge in less than five minutes.
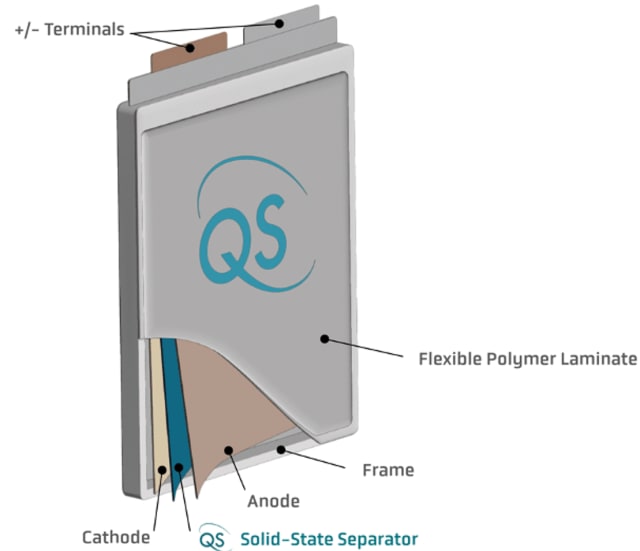
Recent tests conducted on these solid-state batteries at PowerCo’s battery laboratories in Salzgitter have shown impressive results: over 1,000 charging cycles on EV batteries with a range of 500 to 600 kilometers. These batteries maintained 95% of their initial capacity, translating to robust performance over more than half a million kilometers. The ultimate objective is to achieve high energy density, reduce material costs and simplify the manufacturing process.